在复合材料制造中,最终目标是生产一种压实良好的层压板,该层压板具有规定的树脂纤维比并且没有空隙或缺陷。使用预浸料层压板实现这一目标的常见问题包括表面孔隙率、空隙、富含树脂的区域、桥接和其他缺陷。这些通常可归因于材料选择、叠层和/或装袋程序、工具以及有时设计方面的问题。
织物形式的影响

平纹织物表面是最严重的问题,但不是唯一容易出现表面孔隙的织物形式。3K 平纹碳纤维织物看起来像防蚊纱(图1)。交叉点的位置本来就是开放空间,直到在预浸过程中涂上树脂。如果稍后将这种树脂从这些位置拉开,就会出现空隙或多孔区域。


(图2)说明了两种不同类型的织物表面以及两种织物形式之间空隙大小的对比。这是一个实例,说明使用替代织物形式进行设计可以如何最大限度地减少表面孔隙率。
蜂窝夹芯板
在共固化过程中,蜂窝芯在真空或压力下的毛细作用倾向于将树脂从表面层移向芯,从而导致与每个芯单元相邻的多孔表面状况。在表皮与核心界面添加粘合剂可能有助于减少孔隙率,但会显着增加结构的重量。
对于 2-4 层平纹织物表皮尤其如此,其中存在很少的额外树脂(~40% 体积分数)。解决方案可以像在设计中添加超轻表面层1层一样简单,而不是不断地重新加工这些表面。重量损失远小于额外的粘合剂,与重新加工多孔表面的努力、成本和时间相比,风险最小。在任何真空袋压实步骤过程中还必须小心,以在安装芯之前保持表皮层中的树脂含量。
许多复合材料制造商大多忽略了一个事实,即表面孔隙率可能与脱模表面的极低表面能 (SE) 相关,导致树脂排斥而不是润湿表面,从而导致不想要的或过多的孔隙率。这可以通过选择具有更高 SE 的“可调”脱模系统来缓解,该系统能够润湿但仍确保从模具表面脱模。
如果在零件的特定区域反复发现孔隙,这可能是由于模具中与缺陷区域相邻的扩散泄漏。这就需要对模具进行进一步的评估和修理或更换。从边缘呈扇形散开的随机位置的多孔区域可能是由于袋子(或褶皱)中的泄漏而导致的,这可以通过更好的袋子密封轻松修复。
另一个问题是(金属)工具的低传热率,其中袋边层开始胶凝,而工具表面层刚刚变得活跃,导致表面滞留空气或气体。仅在固化配方中添加在真空下的延长停留时间可以解决问题。
角和桶桥接
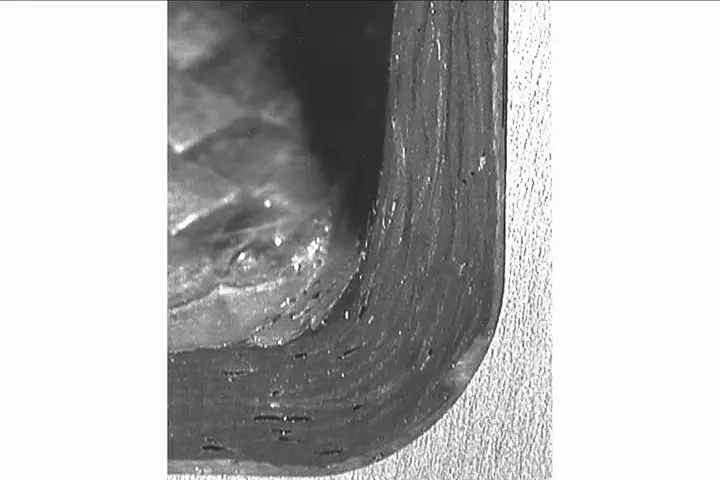
表面孔隙和空隙也可能出现在零件的小半径或较大的凸面区域(模具中的凹面),其中在角落处出现桥接(图 3),或在模具中的层跨越山谷(桶桥)的地方。层间缺乏局部压实和低压区 (LPA) 的产生会导致层压板中富含树脂的区域或空隙。减轻这些缺陷需要仔细检查层板尺寸、放置方法和减厚数量。还必须始终定制剥离层、薄膜和透气层,并确保有足够的袋薄膜(褶皱),以便在减积和固化过程中压实一切(图 4)。

认为高压釜压力会克服桥接缺陷是错误的,例如,考虑典型的高压釜压力为 45-100 psi,而标准模量碳纤维拉伸强度为 ~660 psi。
固化过程中释放气体
固化过程中在层压板中产生气体并不少见,并且会产生有问题的空隙,但您使用的气体缓解策略取决于气体来源。预浸料叠层中水分膨胀的气体通常可以通过在固化前进行更长时间的简单减瘤来缓解。然而,固化过程中树脂中发生的化学反应产生的气体更难以减轻。与环氧树脂不同,酰亚胺、酚醛树脂和聚苯并恶嗪会产生气体副产物,因此需要更深入地了解这些反应才能解决这些问题。
预浸料树脂的热重分析 (TGA) 可用于识别特定温度下与气体释放相关的重量变化。使用此数据,您可以调整固化配方以改变升温速率和等温停留时间,从而留出时间让气体逸出并找到离开层压板的路径。然后,对真空和压力步骤的相应调整将使气体有时间排出或转化回溶液中(图 5)。
新材料开发

传统上,非高压釜 (OOA) 友好型织物的一侧涂有树脂 – 另一侧是干燥的 – 为空气和气体在加工过程中逸出提供内部通道。例如,全厚度可渗透预浸料 (TTPP),该预浸料在树脂薄膜本身中具有均匀的开口间距(即,产生干纤维 LPA),允许层压板内部注入(图 6))。像这样的更多发展将导致材料本身产生低空隙层压板。

将修改转化为最佳实践
建议工程师和技术人员采用系统的方法来解决这些问题,在进行更复杂的更改(例如调整固化配方或添加新材料)之前,首先探索对铺层、减体积和装袋操作的简单修改,这最终可能需要设计和/或材料和工艺规范的更改。未来,鼓励设计师探索使用最适合适用工艺的织物形式和新材料。现在有条不紊地关注细节肯定会带来好的结果,这些结果可以转化为可以在车间重复的最佳实践。